3, 如何开展好车间现场改善
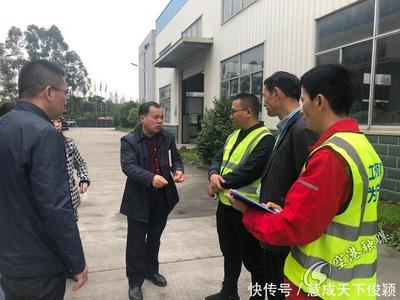
一,组成由某某为总负责,各车间调度为次负责的日常检查制。对日常班组的运作状态作点评。目的是做到生产运行常态化。对检查出来的结果进行处理,在不占用正常上班的情况下(接班后)由问题责任人对问题进行改善,做到当天的问题当天处理完毕方能下班。二,全面推行以班组为单位的早会制。早会的内容有生产的点评和生产的安排。务求达到每一位员工都知晓公司的理念以及工作的质量。三,推行区域划分,分工管理的办法。在车间划分各机台的责任区域,包括固定区域和运动区域。固定区域是指操作机台及工作台辅料区域等。固定区域必须是班组长负全责。运动区域分通道,各机位间的安全距离以及半成品存放区域。这部分可以用班组轮流的方式或指定具体的负责人负责。四,推行产品的标识,标注制度。(附表)标注包括机器设备,区域名称,(设立娃哈哈半成品,成品,胶版,模板,油墨等专区)等。五,纵向管理,横向沟通。本部门的具体工作由负责人执行。公司各部门检查发现的问题交本部门分析,并制订相应的整改措施并负责执行。车间整改是需要请外面的专家来做的,自己做没有专业知识很难做。
4, 车间合理化建议。
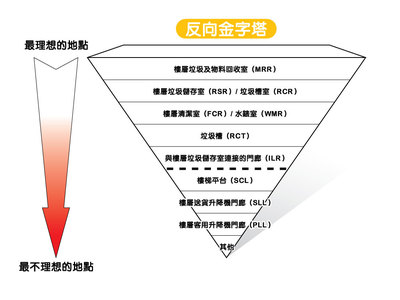
合理化建议:1. 完善的质量管理程序。各班组应严格执行岗位操作法,认真履行自己的职责,相互配合、协调工作。关键控制点要按岗位工艺操作法的规定严格执行、控制,对出现的异常情况,要查明原因,及时排除,使质量始终处于稳定且受控的状态。2. 严格的工艺管理制度。严格执行生产工艺规程,任何人不得擅自变更。对新工人和工种变动人员进行岗位技能培训,经考核合格并有熟练工人指导方可上岗操作,生产车间要不定期检查工艺参数执行情况。3. 重中之重的安全生产管理。经常开展安全活动,弄好班例会,不定期进行认真整改、清除隐患。贯彻安全第一,以人为本预防为主的安全理念。按规定穿戴好劳保用品,认真落实安全防护措施。4. 保证车间安全生产工艺的劳动纪律。车间可依据公司制度,详细制定管理细则,做到奖罚分明,考核方案科学、齐全,处理公开、公正、公平。严格现场管理,要做到生产任务过硬,管理工作过硬,劳动纪律,思想工作过硬。5. 细致的工具管理。个人长期使用的工具做到领用与实物相符,丢失赔偿,各种工具工件按规定使用,严禁违章使用或挪作他用。精密、贵重工具、零件应严格按规定保管和使用。
6, 工厂工作环境改善或建议
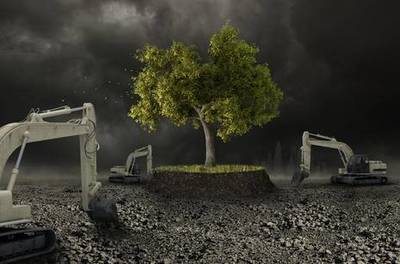
车间生产管理改善的步骤:1、收集问题的记录,并填写《调查表》。2、召开诸葛会议,集思广益,针对问题分析原因(可采用“排列图法”“因果图法”),提出和论证纠正措施或改善 措施的可行性和不可行性,获得共识后,制订《对策表》(对策表的内容包括:分类问题、现状、目标、措施、地点、部门、执行人、完成期限等)。3、布置执行,落到实处。定期检查、监督、评价。4、验证和总结。验证措施的适宜性、符合性、有效性,总结改善过程的经验和不足,为持续改进奠定基础。进行安全生产现场基础知识教育:1、据车间的具体情况,对一些重点工序和存在着较危险因素的重点工序进行针对性的现场基础知识的教育和监督。2、进行基本技能培训,让工人对本工序的工作达到最熟练的程度。要确保时刻都安全生产,单是有安全知识是不够,还必须要有精湛的技能,熟练的动作。在工作的过程中,把握好一种“度”,充分了解设备的性能、环境的变化,从而避免安全事故的发生。3、小问题,大注意。对车间里发生的每一件安全事故或存在的危险因素,例如车间板材边毛刺刮伤手、地板上铁钉子钉伤脚、裸露的电线,看似是小问题,但是会给许多工人带来不经意的伤害,给车间带来潜在的危险。车间应引起注意,及时给工人现场教育,彻底的排除车间的安全隐患,防患于未然。
名词解释
班组
班组是企业中基本作业单位,是企业内部最基层的劳动和管理组织,班组在现在企业中也多按照“最小行政单元”来进行划分。在一般企业里,班组长不算“干部”,但实际上,班组长基本具备了“干部”的管理职能。因此,班组长也被称为“兵头将尾”。现代企业的管理结构一般都是三角形样式,基本上可以分为三层,即决策层(高层)、执行层(中层)、操作层(基层)。高层“动脑”,中层“动口”,基层“动手”,也正是如此,基层因管理需要,而形成的班组最为普遍。
车间
车间,里面有生产的机械设备,体力劳动的工人,产品都是从那里出来的,那就是生产车间。